Sustainable construction with concrete release agents from FUCHS
Sustainability in the construction industry
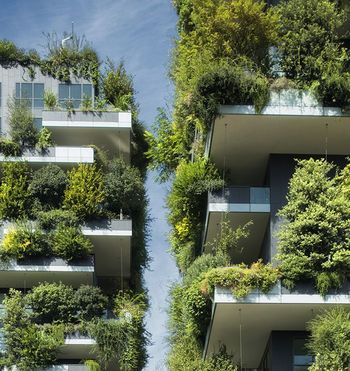
Sustainability has evolved from a trendy topic to a basic requirement in construction projects. The responsible use of natural resources, the minimization of energy requirements and environmental compatibility are more in focus today than ever before.
In order to be able to prove sustainable construction, the following official verifications in particular have become established in the German construction industry:
- DGNB certification
- QNG seal
- EU Ecolabel
Sustainability in the concrete and cement industry
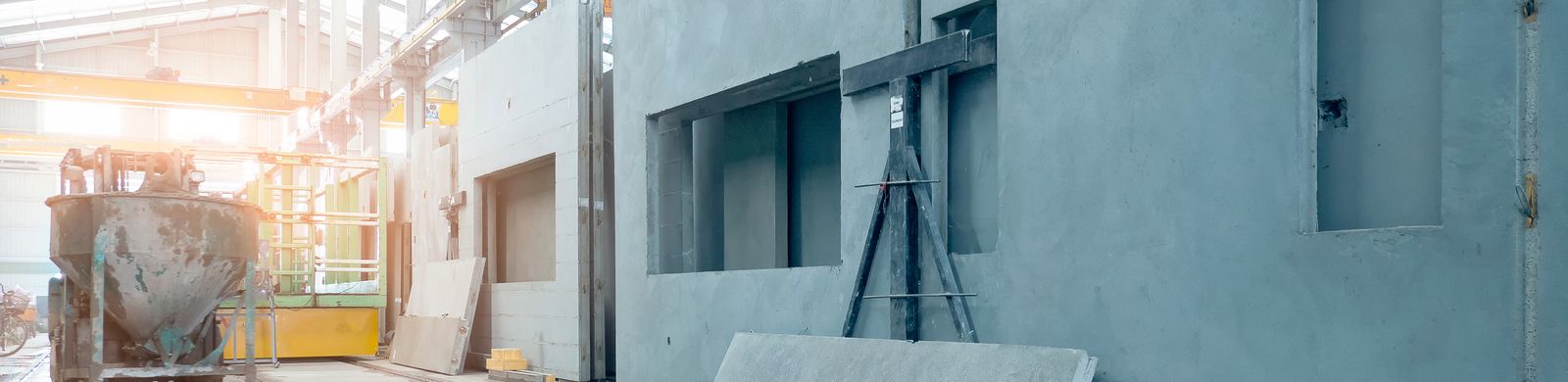
CO2 emissions in cement production
As an essential component of concrete, mortar or screed, cement is a versatile binder and one of the most widely used building materials worldwide. The cement industry is one of the most energy-intensive sectors and therefore bears a special responsibility in climate protection. For many years, efforts have been made to reduce CO2 emissions and conserve natural resources.
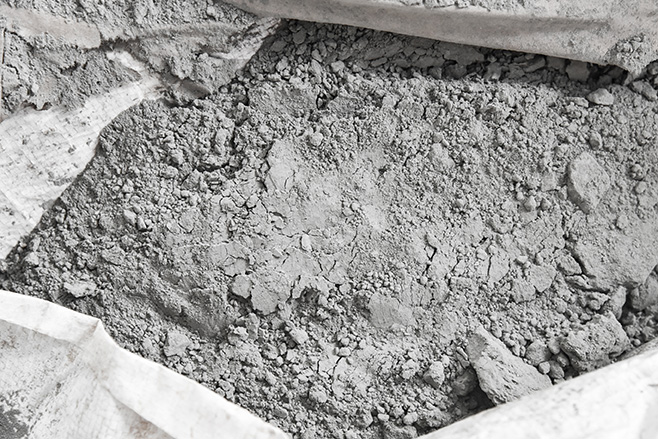
The production of one ton of cement in Germany is associated with CO2 emissions of around 600 kg - around two thirds of which are attributable to raw material-related process emissions, and only one third to fuel emissions. In total, CO2 emissions from the cement industry in this country currently amount to around 20 million tons, which corresponds to around 2% of national CO2 emissions (source: VDZ - Verein Deutscher Zementwerke e.V.).
CO2 reduction today and in the future
For many decades, CEM I cements were the definitive cement type in Germany. A reduction of the emission-intensive cement clinker in the cement is now technically possible, but depends to a considerable extent on the availability of suitable alternative raw materials such as limestone powder, granulated blast furnace slag, fly ash or burnt clay. Currently, CO2 reduced CEM II cements such as CEM II/A-LL cements with limestone powder are frequently used.
For the future, further reduction potentials along the value chain "clinker-cement-concrete-structure-demolition" must be included in order to be CO2-neutral by 2050 in accordance with the EU requirement. This includes, among other things, the use of particularly CO2-efficient cement types such as CEM II/C and CEM VI, which have an even further reduced clinker content.
The resource-saving use of concrete in buildings through leaner construction methods (e.g. with carbon concrete) and the development of new types of mineral binders are further building blocks on this path. These options are also relevant because alternative raw materials will disappear in the long term or will no longer be available in sufficient quantities. These include fly ash, the availability of which is steadily decreasing due to the end of coal-fired power generation, and granulated blast furnace slag as a waste product of today's steel production.
Requirements for the concrete release agents to be used
Due to the changes within the concrete and cement industry and the focus on clinker-reduced cements, new challenges are constantly arising in the production of concrete components and thus also new requirements for the concrete release agents used.
The use of blastfurnace slag containing sulfite, for example, increases the risk of corrosion in steel formwork, and the use of limestone powder increases the risk of lime efflorescence. The cement used has a significant influence on the quality of the concrete surface and on the potential formwork structure, and it is imperative that it be coordinated with the concrete release agent.
At FUCHS, we keep an eye on both current and future developments and work together with our customers to develop the concrete release agents of the future.
Sustainability management at FUCHS
Environmental awareness and sustainable production processes represent a major challenge for many companies. However, we at FUCHS do not see sustainability as a mere responsibility, but as an opportunity. For us and for our customers.
As part of our sustainability strategy, we are continuously working to reduce our emissions. In doing so, we take into account the entire value chain of our products - from the extraction and manufacture of raw materials to the production of our products and their possible recycling. Already in 2020, all FUCHS production sites became gate-to-gate CO2 neutral. This was extended to all subsidiaries and joint ventures in 2021. By 2025, the expansion to worldwide cradle-to-gate CO2 neutrality will take place.
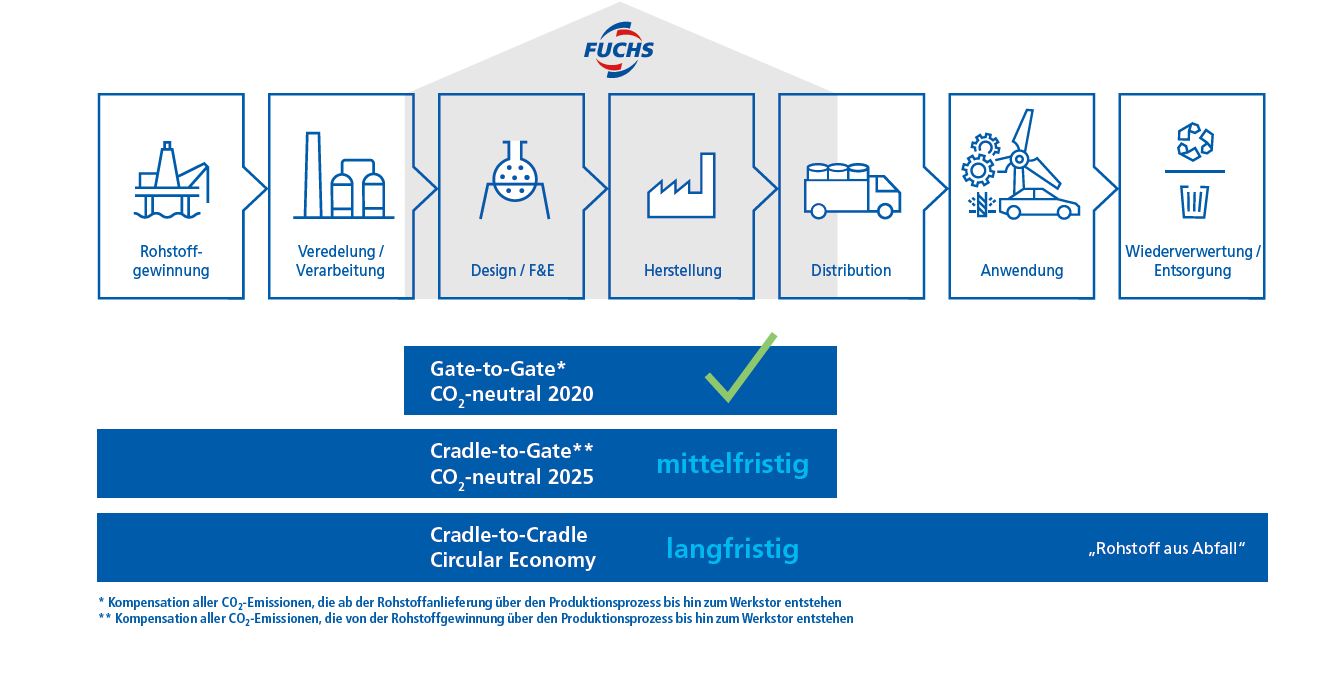
Calculation of the carbon footprint of FUCHS products
TÜV certified method
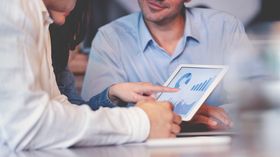
The calculation of the carbon footprint is playing an increasingly important role in the measurement of product emissions. This is because the so-called PCF (Product Carbon Footprint) summarizes all emissions along the value chain that can be associated with the product.
Such a PCF calculation is based on the ISO 14067 standard, which provides uniform regulations for sector-specific standards. However, since no sector-specific standard yet exists for lubricants and release agents, FUCHS developed its own transparent methodology for PCF calculation, which has been officially certified by TÜV.
With the publication of the corresponding methodology document, FUCHS has taken an important step towards defining the procedure for a CO2 calculation and thus showing our suppliers the form in which we require relevant data from them.
Concrete release agents from FUCHS - sustainable & efficient
Sustainability and quality are not mutually exclusive - we prove this with our extensive portfolio of concrete release agents. The concrete composition, the demands on the concrete result and the conditions in the precast plants are usually very individual. This also requires an individual examination of which of our sustainable concrete release agents is suitable for the respective application.
No matter how the concrete composition will develop in the future: We at FUCHS will provide the right concrete release agent for every new challenge or develop it together with our customers.