Mega casting: die-casting process revolutionizes car manufacturing
From many individual parts to one large component
A car consists of many different parts. For decades these components have had to be produced in various processes, then stored, transported and finally assembled. As a result, this consumes an enormous amount of money, energy and time. Mega casting or giga casting means the die-casting process for the production of oversized metal parts specifically for car body manufacturing. This process can save up to 70 parts for each large part. Mega casting saves resources, makes processes leaner and will permanently change the future of automotive manufacturing.
Tesla is the pioneer of this technology. But other car manufacturers are also in the process of adapting their plants to mega casting. Volvo Cars and Volkswagen recently announced that they will switch to mega casting technology in their new production plants for electric cars.
As the first lubricant supplier we can provide our comprehensive product portfolio to cover all your lubricant needs in mega casting.
How does die-casting work?
During the die casting process metal is melted and pressed under very high pressure into a reusable die casting mold. Before the molten metal is pressed into the mold a lubricant or release agent is sprayed into the mold in a thin layer to allow separation. After the component has solidified it is removed from the mold and then passed to the downstream machining processes.
We offer the right lubricants for mega casting process
For pressure die casting and other casting operations, a comprehensive, high quality product range is available. The products of the LUBRODAL range cover the whole process from ladle coatings over plunger lubricants to release agents and also auxiliary products like assembly pastes, ejector lubricants or anti-soldering pastes.
The release agents of the LUBRODAL series ensure excellent releasing, high tool life and best part quality. Wetting, lubrication and cooling have been taken to account during development as well as economics. Due to high dilution ratios, our release agents enable an efficient way of working and prevent residues on the part or in the tools.
We are the only supplier who can cover the entire lubricant demand in die casting including the downstream processes. From hydraulic oils, maintenance oils and industrial oils to greases, release agents and cooling lubricants - we have the right lubricant for you.
FUCHS lubricants are efficient, economical and sustainable
LUBRODAL release agents have good flow properties and therefore spread quickly in a thin layer on the casting mould. These lubricants do not form any protruding substances or residues in or next to the moulds and sticking of the ventilation slots does not occur.
LUBRODAL lubricants minimize friction and wear and ensure the highest component quality, increased process reliability, reduced operating costs and lower environmental impact. As we can cover all your lubricant needs, transport supply chains are reduced and therefore CO2 is also reduced.
YOUR ADVANTAGES AT A GLANCE
- comprehensive lubricant portfolio from a single source: from release agents and assembly pastes to piston lubricants
- intensive consulting and on-site support by our service engineers
- customized lubricant solutions to meet your needs
- more safety, as our products do not cause smoke and are non-flammable
- sustainable, as the functional life of your molds will be extended
- reduction of your total cost of ownership (TCO)
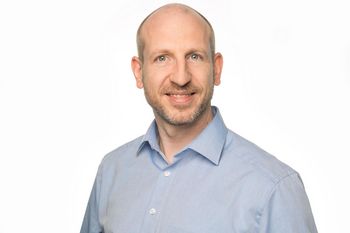
'Mega casting is revolutionizing car body manufacture. As a global full-solution provider FUCHS offers the right lubricants for all pre- and post-processes as well as hot forming lubricants for the casting process itself.'
Andreas Degel, Product Manager Hot Forming Lubricants